Optimierte Konzepte für die Eisenbahn von morgen
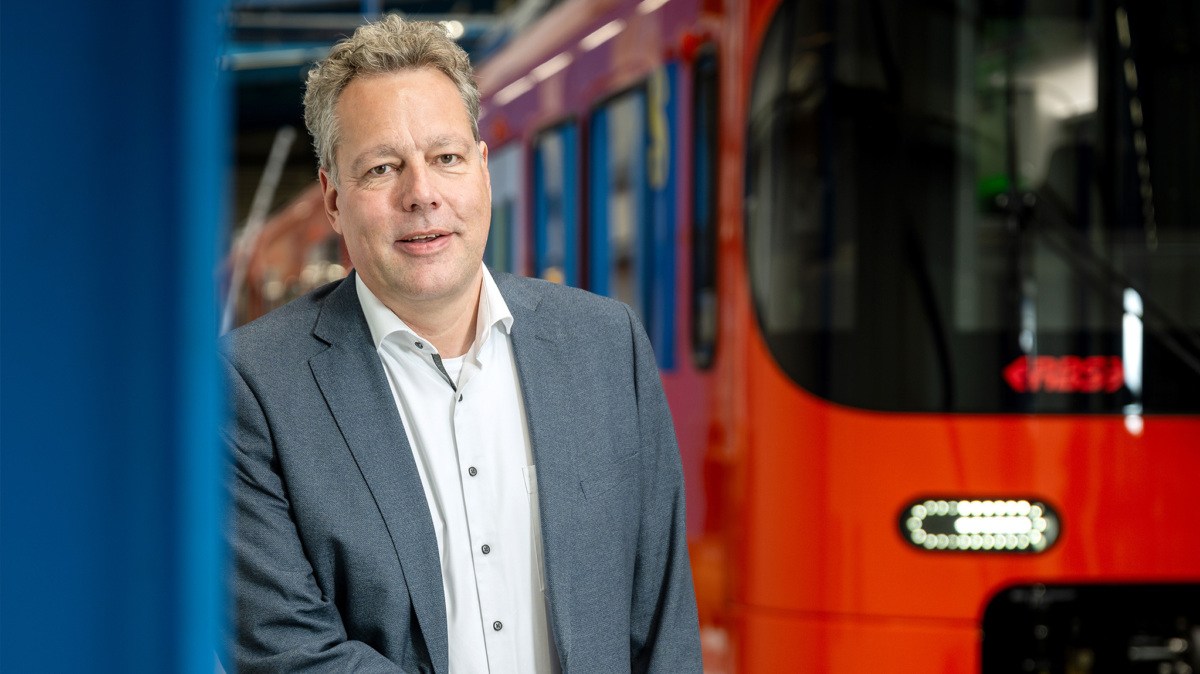
Eisenbahnen, das weiss jedes Kind, sind per se das umweltfreundlichste Verkehrsmittel. Warum das so ist, kann Ansgar Brockmeyer (Bild), der Divisionsleiter Verkauf und Marketing sowie stv. Group CEO von Stadler, erklären: «Dafür gibt es drei technische Gründe: Erstens fährt ein Zug mit einem Stahlrad auf einer Stahlschiene; das hat den Vorteil einer sehr niedrigen Reibung. Zweitens macht ein Zug das, was auch Radrennfahrer machen: Er fährt im Windschatten. Nur das erste Fahrzeug muss den aerodynamischen Luftwiderstand überwinden, die anderen fahren im Windschatten. Und drittens ist die Eisenbahn spurgebunden; man kann sie also relativ einfach elektrifizieren und den Zug so lokal emissionsfrei machen.»
In einem Bahnland wie der Schweiz werden diese Vorteile genutzt. Das Netz ist vollständig elektrifiziert; mit Ausnahme weniger Rangierfahrten oder sporadischer Museumszüge fahren alle Personen- und Güterzüge zu 100 Prozent elektrisch. «Da ist die Schweiz einzigartig», sagt Brockmeyer. «Auch deshalb ist ‹Swiss Made› in anderen Ländern ein gutes Argument.» Nicht überall sind aber Schweizer Gegebenheiten mit engen Zugfolgen in dicht besiedelten Agglomerationen und überall verfügbarem Strom anzutreffen. Deshalb erarbeitet Stadler seit jeher individuelle, auf die Kundenbedürfnisse angepasste Lösungen. Früher war dies fokussiert auf die Herstellung von Rollmaterial; inzwischen bietet Stadler ganze Konzepte an.
«Wir können unter einer Oberleitung elektrisch fahren und während der Fahrt die Batterie laden.»
Effiziente Teilelektrifizierung
«Was Stadler aktuell in einigen Ländern empfiehlt, ist die Teilelektrifizierung einer Strecke», sagt Ansgar Brockmeyer. Er verweist auf ein aktuelles Beispiel in Norwegen, einem der wichtigsten Märkte des Schweizer Zugbauers: Vor allem im Süden des Landes mit grösserer Bevölkerungsdichte sind seit vielen Jahren mehrere Generationen von Flirt-Kompositionen («flinker leichter Intercity- und Regional-Triebzug») als Regional- und auch als Fernverkehrszüge im Einsatz, «die Hälfte der etwa 300 aktuellen Regionalzüge sind Flirt von Stadler» sagt Brockmeyer, «auch die nächste Generation der Fernverkehrszüge hat die norwegische Bahn bei uns bestellt.» Viele dieser Züge werden unter einer Oberleitung fahren; einige der 200 Stundenkilometer schnellen Flirt Nordic werden aber trimodal ausgelegt, sie können elektrisch, mit Dieselaggregat oder mit Batterie fahren. In dem grossen Land gibt es noch etliche Strecken, die nicht elektrifiziert sind.
Das gilt auch für die Nordlandsbanen, eine über 700 Kilometer lange Linie zwischen Trondheim und Bodø im weniger dicht besiedelten hohen Norden Norwegens. Heute machen sich dort in jeder Richtung täglich zwei Personenzüge auf die fast zehnstündige Fahrt. Im Güterverkehr sind es etwas mehr Züge; die Nachfrage steigt. Alle Züge fahren im Dieselbetrieb. «Da laufen Stadler Euro-Dual-Lokomotiven im Diesel-Modus, deshalb kennen wir die Strecke sehr gut», erklärt Ansgar Brockmeyer, «es gibt viele Berge, Brücken und auch Tunnels, die schwierig zu elektrifizieren wären.» Stadler wurde wie auch andere Hersteller eingeladen, ein Konzept für einen klimaneutralen künftigen Betrieb der Strecke vorzuschlagen. Andere Anbieter haben Lösungen mit Wasserstoff eingereicht oder auch eine durchgehende Elektrifizierung vorgeschlagen. Stadler hat ein Konzept entwickelt, das eine Batterie-gestützte Lösung vorsieht – auch, weil entlang der Strecke nicht überall Strom verfügbar ist.
Die wirtschaftlichste Lösung
«Über die Strecke verteilt sind etwa 40 Abschnitte mit Oberleitung vorgesehen», erläutert Ansgar Brockmeyer. Diese Strom-Inseln sind oft dort, wo es Steigungen hat, die den Energiebedarf eines Zugs erhöhen; so kann der Antrieb direkt mit Strom versorgt werden, während gleichzeitig die Batterie geladen wird.
Die norwegische Eisenbahndirektion hat alle Konzepte analysiert und die Wirtschaftlichkeit geprüft, «die Norweger haben unser Konzept ausgewählt. Das wird nun in den norwegischen Verkehrswegeplan geschrieben».
Je nach Auslastung einer Strecke sind oft hybride Konzepte am besten, das müsse aber man jeweils im Einzelfall untersucht werden, wie Brockmeyer betont. «Für die Nordlandsbanen ist die Teilelektrifizierung die wirtschaftlichste Lösung.»
Verdient hat Stadler mit der erfolgreichen Vermittlung dieser Erkenntnis noch nichts. «Wir haben uns am Ideenwettbewerb beteiligt, um mit einem optimalen Konzept das Vertrauen in uns zu stärken.» Freilich: Wenn demnächst basierend auf diesem Konzept ein neuer Auftrag ausgeschrieben wird, kann Stadler Fahrzeuge konfigurieren, die diesen Anforderungen entsprechen dürften: Triebwagen aus der erfolgreichen Flirt-Plattform, aber auch verschiedene vier- und sechsachsige Lokomotiven, die während der Fahrt unter Oberleitung Akkus aufladen, die dann auf fahrdrahtlosen Abschnitten die Antriebsenergie für die Elektromotoren liefern.
«Alle Zahlen kommen auf den Tisch. Damit gibt es zum Glück keinen Ideologie-Streit.»
Fahren und gleichzeitig laden
Züge mit Batterien gibt es in der Eisenbahngeschichte schon lange. Die Preussische Staatsbahn bestellte bereits 1907 Akkutriebwagen für Nebenbahnen; Argumente waren damals primär die niedrigen Betriebskosten. Erst in den 1980er-Jahren sind die letzten Akkutriebwagen vom deutschen Schienennetz verschwunden. Bis Stadler die Idee mit einer modernen Interpretation wiederbelebte – und dabei auch an die eigene Geschichte anknüpfte: Ernst Stadler fing 1943 mit dem Umbau von Feldbahnlokomotiven auf Batteriebetrieb an und legte so den Grundstein für das heutige Unternehmen.
Die heutigen Batteriezüge unterscheiden sich allerdings in wesentlichen Punkten von den historischen Vorgängern, insbesondere die Batterietechnik hat sich weiterentwickelt. Das machte viele Innovationen möglich, wie Ansgar Brockmeyer erklärt: «Klassische Batteriezüge konnten nur im Depot geladen werden und hatten keinen Stromabnehmer. Wir können unter einer Oberleitung elektrisch fahren und während der Fahrt die Batterie laden.»
Auch interessant
Weltrekord für Batteriezug
In Deutschland bot sich Stadler unverhofft eine gute Gelegenheit, Erfahrungen mit Batterie-Zügen zu sammeln: «Wir haben einen verunfallten Flirt repariert und damit den ersten Prototypen eines Batteriezugs gebaut», sagt Ansgar Brockmeyer. Mit Erfolg: Die Erfahrungen mit dem neuen Konzept wurden auch vom Guinness-Buch der Rekorde dokumentiert; Ende 2021 fuhr der Flirt Akku 224 Kilometer im reinen Batteriemodus, was Weltrekord bedeutete.
Inzwischen stehen seit dem Fahrplanwechsel 2023 die ersten serienmässigen Batteriezüge Europas im Einsatz. In Deutschlands hohem Norden beteiligte sich Stadler an einer technologieoffenen Ausschreibung für die bisherigen Dieselstrecken des Nahverkehrsverbunds Schleswig-Holstein GmbH. Denkbar wären auch Wasserstoff-Lösungen oder eine durchgehende Elektrifizierung gewesen; die Kosten für Tankstellen oder die Oberleitung waren im Angebot aber einzukalkulieren. Wie später in Norwegen schlug Stadler auch hier eine Teilelektrifizierung vor, «einzelne elektrische Knoten wie den Bahnhof Kiel gab es schon», sagt Brockmeyer, «wir haben zusätzliche elektrische Inseln vorgeschlagen, wo Batteriezüge nachgeladen werden können.» Diese Oberleitungsabschnitte baut jetzt die Netzgesellschaft der Deutschen Bahn, Stadler liefert insgesamt 55 zweiteilige Flirt Akku. «Unser Konzept war in der Gesamtschau das wirtschaftlichste und effizienteste.» Und damit eben auch das nachhaltigste.
Strategische Entscheidungen
«Als wir gesehen haben, dass es am Markt tatsächlich ein Potenzial für alternative Antriebe gibt, sind wir strategisch an das Thema gegangen», sagt Ansgar Brockmeyer. Verwaltungsratspräsident Peter Spuhler stellte seinem Team die Aufgabe, eine Produktstrategie für die alternativen Antriebe zu entwickeln. Die Produktentwicklung und der Verkauf nahmen den Ball auf. Bald stellte sich heraus, dass Stadler für längere nicht elektrifizierte Strecken als Diesel-Alternative auch ein Wasserstoff-Fahrzeug im Portefeuille braucht. Fast zeitgleich kam eine konkrete Anfrage aus Kalifornien, wo Stadler gerade Flirt mit Dieselantrieb ablieferte. Die Kalifornier wünschten, dass ein Fahrzeug mit Wasserstoff-Antrieb ausgelegt werde, um zu zeigen, dass das funktioniert.
«Das haben wir gemacht, aber nicht als Prototypen wie beim Batteriezug, sondern als erstes Fahrzeug einer neuen Plattform», erklärt Ansgar Brockmeyer. Das bedeutet, dass die im gewünschten zweiteiligen Flirt eingebaute Antriebstechnik so skalierbar ist, dass damit auch andere Züge ausgerüstet werden können. «Das stellte sich als kluge Entscheidung heraus, denn als Kalifornien Wasserstoff-Züge nachbestellte, wurden vierteilige Züge geordert.»
Die Wasserstoff-Flirt haben ein kurzes Mittelteil, das optisch an die seinerzeitige Lösung bei den Gelenktriebwagen erinnert. In diesen zusätzlichen «Powerpacks» ist die Wasserstoff-Technik verbaut, der restliche Zug – Batterie, Antriebstechnik, Stromrichter – entspricht einem Flirt Akku. Eine Batterie ist für den Wasserstoffbetrieb zwingend notwendig: «Die Brennstoffzelle kann man nur sehr gleichmässig belasten, deshalb braucht es immer eine Pufferbatterie.» Sollte die Strecke in Kalifornien dereinst elektrifiziert oder auch nur teilelektrifiziert werden, kann das Powerpack aus dem Triebzug entfernt werden, der Zug ist dann ein Flirt Akku. Was der Flirt H2 zu leisten vermag, steht inzwischen ebenfalls im Guinness-Buch der Rekorde: Im März fuhr die zweiteilige Komposition 46 Stunden lang ohne nachzutanken eine Strecke von 2803 Kilometern.
Zusätzliches Wissen im Team
Wenn alternative Antriebe gefragt sind, verschiebt sich die Schnittstelle zwischen dem Betreiber und dem Hersteller. «Wir als Hersteller müssen viel mehr Betreiber-Wissen haben», sagt Ansgar Brockmeyer. «Wir müssen die Infrastrukturdaten der Strecke haben, damit wir das rechnen können, und eine gewisse Kompetenz, dass wir das rechnen können.» Diese Kompetenz hatte Stadler vor zehn Jahren noch nicht, «da konnten wir Züge bauen, aber den Betriebseinsatz noch nicht selbst analysieren». Inzwischen versteht sich Stadler längst nicht mehr nur als reiner Zugbauer, sondern als Anbieter von Verkehrslösungen. Dafür musste das Team gezielt mit spezifischem Know-how ergänzt werden.
Für eine bestimmte Strecke ein Antriebskonzept zu entwickeln bedeutet, eine Gleichung mit mehreren Unbekannten zu lösen. «Man muss sowohl die Auslegung der Strecke als auch die Auslegung der Fahrzeuge optimieren, um die beste Wirtschaftlichkeit zu erreichen», erklärt Brockmeyer. Dafür muss fallweise auch in die Fahrplangestaltung eingegriffen werden – etwa dann, wenn reine Batteriezüge zwischen zwei Endbahnhöfen pendeln, wo sie nachgeladen werden: Wenn sie im Endbahnhof weniger als 20 Minuten stehen, reicht manchmal die Zeit für eine schonende Ladung der Batterie nicht.
Zentrale Produktentwicklung
Im Gegensatz zu den meisten Wettbewerbern ist Stadler grundsätzlich sehr dezentral organisiert; alle Divisionen haben alle Kompetenzen, die sie benötigen, um einen Auftrag abzuwickeln. Deshalb gibt es auch an vielen Standorten grosse Engineering-Teams. Drei Bereiche allerdings sind zentral organisiert: Neben den Finanzen, damit die kommerziellen Risiken der einzelnen Divisionen kontrolliert werden können, gilt das auch für den Verkauf, damit die einzelnen Divisionen nicht plötzlich in einem Markt als Konkurrenten gegenüberstehen. Auch die Produktentwicklung ist zentral organisiert; sie bietet ihre Dienste für die ganze Gruppe an.
Die Entscheidung, welches Produkt bei einer Ausschreibung jeweils angeboten wird, trifft die Produktentwicklung mit dem Verkauf und dem obersten Management. «Alle zwei Wochen treffen wir uns zu einer Verkaufssitzung, an der auch Verwaltungsratspräsident Peter Spuhler dabei ist. Da werden diese strategischen Fragen miteinander abgestimmt», sagt Ansgar Brockmeyer. «Wenn es um die Auswahl eines Produkts mit alternativem Antrieb geht, dann wird das gerechnet; alle Zahlen kommen auf den Tisch. Damit gibt es zum Glück keinen Ideologie-Streit um die richtige Technologie.»
Auch interessant
«Heute noch einen Diesel-Zug zu kaufen, ist eine schwierige Entscheidung.»
Eine neue Generation RegioShuttle
Im Zuge der Strategieentwicklung kristallisierte sich heraus, dass Stadler ein weiteres neues Produkt in der Angebotspalette benötigen wird: Als 2001 Stadler das Adtranz-Werk in Berlin-Pankow übernahm, kam auch die Lizenz für den RegioShuttle zu Stadler. Von diesen einteiligen Dieseltriebwagen wurden rund 700 Stück gebaut, die eines Tages ersetzt werden müssen. «Für genau diesen Verwendungszweck bauen wir nun einen Nachfolger», verrät Ansgar Brockmeyer, «auf der Innotrans im September werden wir das Fahrzeug vorstellen.» An der Fachmesse für Verkehrstechnik, die alle zwei Jahre in Berlin stattfindet, wird Stadler einen neuen, zeitgemässen und wiederum in Berlin gebauten RegioShuttle präsentieren: Der Wagenkasten wird in Leichtbauweise aus Aluminium statt aus Stahl konstruiert, trotzdem wird der Triebwagen die inzwischen viel strengeren Crash-Normen erfüllen. Und natürlich werden statt Dieselmotoren jetzt alternative Antriebe vorgesehen; spurtstarke Elektromotoren werden ihre Energie aus einer Batterie oder einem Wasserstoff-Aggregat beziehen.
Viele Dieselstrecken sind nicht elektrifiziert, weil nur wenige Züge verkehren und es deshalb nicht wirtschaftlich wäre. Auf solchen Nebenbahnen ist nicht selten der Oberbau technisch so beschaffen, dass die Achslast der Fahrzeuge auf deutlich unter 20 Tonnen pro Achse begrenzt ist – gerade Züge mit Batterien sind aber meistens schwerer. Der RegioShuttle in Leichtbauweise soll hingegen mit unter 18 Tonnen Achslast für all diese Strecken einsetzbar sein.
Eisenbahnfahrzeuge sind darauf ausgelegt, während 30 bis 40 Jahren grosse Laufleistungen zu erbringen. Einzig Verschleissteile wie Räder müssen in diesem Lebenszyklus mehrfach ausgewechselt werden. Ein Zug ist ein langfristiges Investitionsgut; die Bahnen schreiben ihre Fahrzeuge auf 30 oder 40 Jahre ab.
Diese lange Lebenserwartung eines Zugs bedingt auch eine vorausschauende Flottenplanung. «Inzwischen hat fast jedes europäische Land ein Netto-Null-Ziel, das in einem Zeitraum von weniger als 30 Jahren erreicht werden soll. Deshalb sagt Ansgar Brockmeyer: «Heute noch einen Diesel-Zug zu kaufen, ist eine schwierige Entscheidung.»
Lacke ohne Lösungsmittel
In jüngerer Zeit hat Stadler wie in St. Margrethen mehrere neue Werke gebaut, die ganz andere energetische Massstäbe setzen als ältere Fabriken – und grosse Solaranlagen auf den Dächern haben. Im Innern der Fabriken haben sich viele Produktionsschritte stark verändert, unter anderem wurden vor wenigen Jahren die Lackiereinrichtungen vollständig umgestellt. Heute werden keine Lösungsmittel-basierte Lacke eingesetzt, sondern nur noch Wasser-basierte. «Das war ein sehr schwieriger Prozess, weil die Anforderungen an die Lackqualität sehr hoch sind», sagt Brockmeyer.
Immerhin war Stadler da nicht allein, «die ganze Branche hat Druck gemacht, die Lackhersteller mussten sich etwas einfallen lassen». Für Stadler bestand die Herausforderung darin, alle Fabriken umzustellen. «Wir mussten Spritzkabinen umrüsten, Filter für Wasser und für Luft umstellen oder die Entsorgung neu organisieren.»
«Die ganze Nachhaltigkeitsbürokratie ist nicht nachhaltig.»
Nachhaltigkeits-Bürokratie
Weil Eisenbahnen per se ökologisch sind, bestand bei Stadler noch nie ein Bedarf nach «green washing». Daher erkannte man auch relativ spät erst die Chancen einer Nachhaltigkeitsberichterstattung. Schon lange lässt Stadler auch Managementprozesse auditieren oder die Qualitätssicherung zertifizieren. «Wir haben jede Menge Audits und Qualitätssicherungsthemen, die wir hier bedienen, um die Funktionsfähigkeit unserer Prozesse unter Beweis zu stellen», sagt Ansgar Brockmeyer.
«Jetzt kommt das ganze Nachhaltigkeitsthema noch dazu. Auch hier müssen wir wieder die Funktionsfähigkeit unserer grundlegenden Managementprozesse nachweisen.» Grundsätzlich helfe die Nachhaltigkeitsdiskussion dem Hersteller eines grünen Produkts, «was nicht hilft, ist, dass die Debatte mit ihren Auswirkungen übers Ziel hinausschiesst. Die ganze Nachhaltigkeitsbürokratie ist nicht nachhaltig».
Im Nachhaltigkeitsbericht ist unter anderem festgehalten, dass Stadler-Züge zu 95 Prozent recycelbar sind; würde man die thermische Verwertung der Kunststoffe mitrechnen, kommt man sogar auf 98 Prozent. Das energieintensive Aluminium lässt sich beliebig oft recyceln. Und auch dessen Herstellung kann nachhaltig sein: «Den Aluminium-Produktionsprozess kann ich komplett dekarbonisieren, ich brauche nur Strom und Bauxit», sagt Brockmeyer. «Wenn wir Aluminium kaufen, das mit grünem Strom elektrolysiert wurde, ist dieser Teil des Prozesses CO₂-frei.»
Automatisiertes fahren
Viel hat Stadler in seine digitalen Kompetenzen investiert. Einem strategischen Beschluss folgend, hat Stadler eine eigene Division für Signaltechnik aufgebaut. Früher musste Stadler Zugsicherungs-Technologien ausgerechnet bei Wettbewerbern einkaufen, «da wollten wir unabhängig werden», sagt Ansgar Brockmeyer. «Wir wollten aber nicht nur ein Me-Too-Produkt entwickeln, sondern Digitalisierungs- und Automatisierungslösungen entwickeln, die unsere Konkurrenten so nicht haben.»
Dank eines Computer-berechneten optimierten Fahrbetriebs können Züge, die zwar noch einen Lokführer haben, teilautomatisiert anfahren und bremsen. Dadurch kann ein Fahrzeug bis zu 50 Prozent Energie einsparen.
Die Technologie ermöglicht es auch, Konzepte für Fahrten ganz ohne Lokführer zu entwickeln. Für die zwei Kilometer lange Zahnradbahn zwischen Rheineck und Walzenhausen testet Stadler gerade Radar-Sensoren, die Hindernisse erkennen sollen – die Bahn verkehrt nicht in einem abgeschlossenen System wie eine U-Bahn; es gibt unterwegs Bahnübergänge und weidende Kühe. Stadler kann im Erfolgsfall vor der eigenen Haustüre eine doppelte Referenz vorzeigen: Zum einen, dass das Unternehmen technologisch führend ist – und zum anderen, dass durch den klugen Einsatz der richtigen Technologie eine bisher defizitäre Bahn gerettet werden kann.
Dr. Ansgar Brockmeyer ist Divisionsleiter Verkauf und Marketing sowie stv. Group CEO von Stadler. Der Konzern mit Hauptsitz im thurgauischen Bussnang macht etwa 85 Prozent seines Umsatzes mit Rollmaterial; bereits 13 Prozent steuert die Division Service bei. Das Segment Signalling wächst mit aktuell 700 Mitarbeitern schnell.
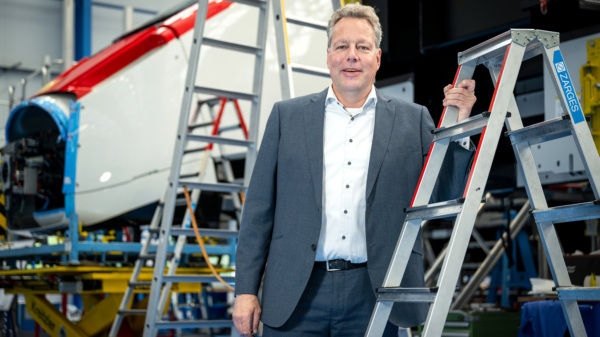
Text: Philipp Landmark
Bild: Reto Martin; zVg