National bahnbrechend: Gepulverte Laseroberflächen
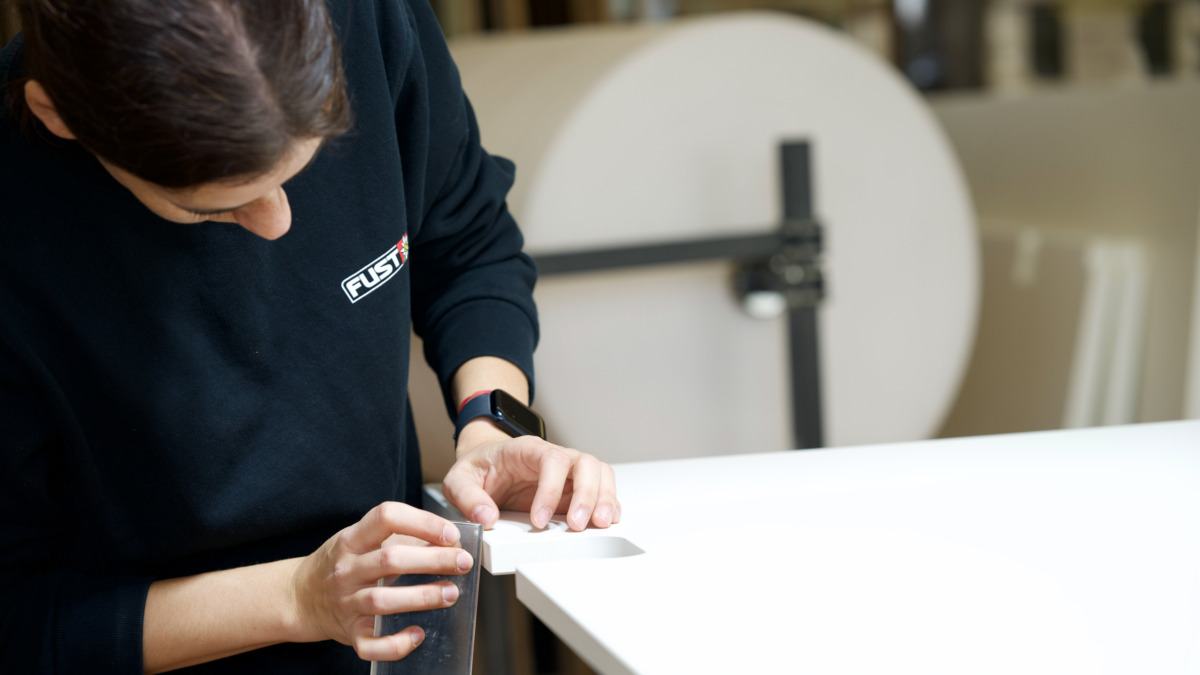
Text: pd
National in Erscheinung traten die Wiler bereits mit der Vorstellung ihrer Online-Schreinerei Ecoleo in «die Höhle der Löwen» sowie mit der Übernahme der Thuner Woodcoat AG, die als nationale Wegbereiterin der Pulverbeschichtung von Holz gilt. Mit der Kombination von Laser und Pulver sorgt die Schreinerei Fust nun wiederholt für Aufsehen.
Von «unmöglich» zu «geht doch»
Laseroberflächen und die nachhaltige Pulverbeschichtung sind junge Technologien der holzverarbeitenden Branche. Beide erfreuen sich einer zunehmenden Beliebtheit. Mit einer Pionierleistung macht die Schreinerei Fust nun die Kombination beider Technologien möglich und bringt pulverbeschichtete Laseroberflächen aus der eigenen Werkstatt hervor.
Mit einem eigens entwickelten, geheimen Verfahren reüssierten die Wiler darin, Pulver in maximaler Detailgenauigkeit auf Reliefoberflächen haftbar zu machen. Ein Novum, das bislang als unmöglich erschien und der Innenraumgestaltung erstaunliche Gestaltungswelten eröffnet. Noch dazu 100% lösungsmittelfrei und mit einem Recyclinggrad des Pulvers von 97%.
Gestaltungsfreiheit dank Pulverbeschichtung
Die gepulverten Laseroberflächen eröffnen kreativen Inneneinrichtern und Architekten schier endlose Gestaltungs- und Individualisierungsmöglichkeiten. Nahezu jedes Sujet kann mittels Laser auf die Oberfläche appliziert und anschliessend mit Eco-1-zertifizierter Pulverbeschichtung in fast allen Farbtönen alltagstauglich gemacht werden.
Die widerstandsfähigen und schadstoffarmen Oberflächen zeichnen sich zudem durch die Realisierbarkeit von Freiformen aus. So können Griffmulden, Gehrungen und andere Gestaltungselemente massgeschneidert gestaltet und nachhaltig geschützt werden.
Gerade bei Küchen- und Schrankfronten sowie im Ladenbau oder Branding von Innenausbauten, beispielsweise bei Empfangsbereichen von Unternehmen, stellt das Verfahren einen bedeutenden Technologiesprung dar. Architekten, Küchenstudios, Schreiner und andere Gestalter können Kunden somit individuelle Designs anbieten.
Erstpräsentation an der OLMA
Am Eröffnungstag der OLMA, Donnerstag, 12. Oktober, enthüllte die Wiler Schreiner um 10 Uhr ihre bahnbrechende Innovation und machte sie erstmals der Öffentlichkeit zugänglich. Auf dem Messestand in Halle 9.1.A, Stand 27 können kreative Köpfe die neue Technologie haptisch erleben.
Designvielfalt, Technologie und ein Spiel mit Licht und Schatten
- Mittels Lasertechnologie entstehen 3D-Relief-Oberflächen mit sehr individuellen Designs.
- Leichte Reliefs in der Oberfläche bewirken eine dreidimensionale, plastische Wirkung.
- Das Spiel mit Licht und Schatten lässt sich mit Streiflicht auf faszinierende Weise verstärken.
- Die Sublimationstechnologie ermöglicht enorm präzise Bearbeitungen, welche bisher nur mit immensem Aufwand machbar waren.
- Das Laser-Schneiden, -Sublimieren und -Gravieren funktioniert für viele verschiedene Werkstoffe wie Holz, Metalle, Kunststoffe, MDF-Platten usw.
- Im Gegensatz zu Fräswerkzeugen entfallen Schärf-Arbeiten, weil die Lichtquelle abnutzungsfrei ist. Das gewährleistet stets gleichbleibende Qualität der Oberflächen.
Arbeitsprozesse der Sublimation mittels Laserstrahl
- Design entwerfen und entwickeln, sehr bedeutender Teil des Sublimationsverfahrens
- 3D-Effekte und Tiefenwirkung mit verschiedenen Graustufen definieren, (weiss = hoch, schwarz = tief)
- Maschine bestücken, Werkstücke positionieren, individuell vorbereitete Vorlagen abrufen
- Bildauflösung und Bearbeitungs-Parameter definieren, Maschine programmieren für Laserleistung, Absaugung, Ausblasdruck, Vorschubgeschwindigkeit (10 bis 3'800 mm/sec.)
- Mögliche Dateiformate: PDF, DXF, JPG, PNG, usw.
- Maximalgrösse: 3000 x 2000 mm, bis 2000 kg belegbar
- Schmauch entfernen, Untergrund haftfähig machen für Pulverbeschichtung, anspruchsvolles Verfahren (Schlüsselkompetenz), gut gehütetes Betriebsgeheimnis
- Die Schneidefunktion sei nur am Rand erwähnt: Auch das Schneiden von Holz, Kunstoffen, Metallen usw. ist möglich, erfolgt mit supergepulster 2KW-Laserquelle
Arbeitsprozesse der Pulverbeschichtung von gelaserten Werkteilen
- Teile in Klimakammer 24 Stunden konditionieren, Holzfeuchte exakt 4,9 - 5,6 %.
- Teile vorbereiten, Bohrlöcher mit Stopfen verschliessen (Schutz vor Überhitzung)
- Teile entstauben, kontrollieren, leitfähig an Wagons aufhängen
- Teile reisen automatisiert durch mehrstufige Beschichtungsanlage
- Teile leitfähig machen: im 350 Grad heissen Preheating-Ofen auf 70 Grad vorheizen
- Durchlaufverfahren mittels Infrarot-Strahler, Restfeuchtigkeit an Kante bringen, notwendig zur Erreichung Leitfähigkeit, sehr heikler Teil des Prozesses
- Grundierungspulver applizieren, Durchlaufverfahren mit Lichtschrankensteuerung, automatisierter Auftrag des Grundierungspulvers mit Sprühpistolen, Primer-Pulver ist Fundament des powder-coatings, Qualitätspulver von IGP-Switzerland bietet besten Haftgrund, überbrückt Spannungen im Holz optimal, gewährt hervorragenden Schutz auf Fläche und Kanten, Herausforderung: exakte Schichtstärken erzielen auf Kanten und Flächen
- Grundierung aushärten, Pulververnetzung im 350 Grad heissen, 13.5 Meter langen Durchlaufofen bis zur vollständigen Aushärtung
- Grundierung prüfen, regelmässige akkurate Laboranalysen auf perfekte Schichtstärke und Unregelmässigkeiten, Grundierung ist Basis für hochqualitative Endergebnis
- Deckpulver applizieren, unmittelbar nach kurzen Auskühlfase durchlaufen Teile die Anlage ein zweites Mal automatisiert, Applikation Deckpulver im gewünschten Farbton. Der Beschichtungsvorgang ist abgesehen von der Schichtstärke identisch mit dem der Grundierung.
- Deckpulver aushärten im Durchlaufofen während 5 Minuten bei 350 Grad, höchst anspruchsvoller Vernetzungs-Prozess, nur fertig ausgehärtetes Pulver ist mechanisch und chemisch maximal belastbar
- Teile abkühlen, 125 Grad Oberflächentemperatur bei Ofen-Austritt, Teile durchlaufen aktive Kühl-Zone, Abwärme heizt Produktionshallen.
- Teile abhängen, anhand eingefräster Teileidentifikationsnummern etikettieren, unter Top-Lichtverhältnissen sehr gründlich kontrollieren,
- Labortests durchführen, tägliche Referenz-Muster mitproduzieren, Messen von MDF-Feuchte, Schichtstärke, Aushärtungsgrad, chemische Beständigkeit, Kratzfestigkeit, wöchentlich Feuchtebeständigkeit der Beschichtung in aufwendigem Verfahren testen, Massnahmen garantieren gleichbleibende Beschichtungsqualität, tägliche Rückstellmuster archivieren
- Fertige Pulverteile kommissionieren, für eigene Kunden in interne Corletten stellen, für externe B2B-Kunden auf Palletten stapeln, verpackungsreduziert gut schützen, schweizweit per Cargo Domizil umweltfreundlich spedieren